Nabeshima Ware
鍋島焼
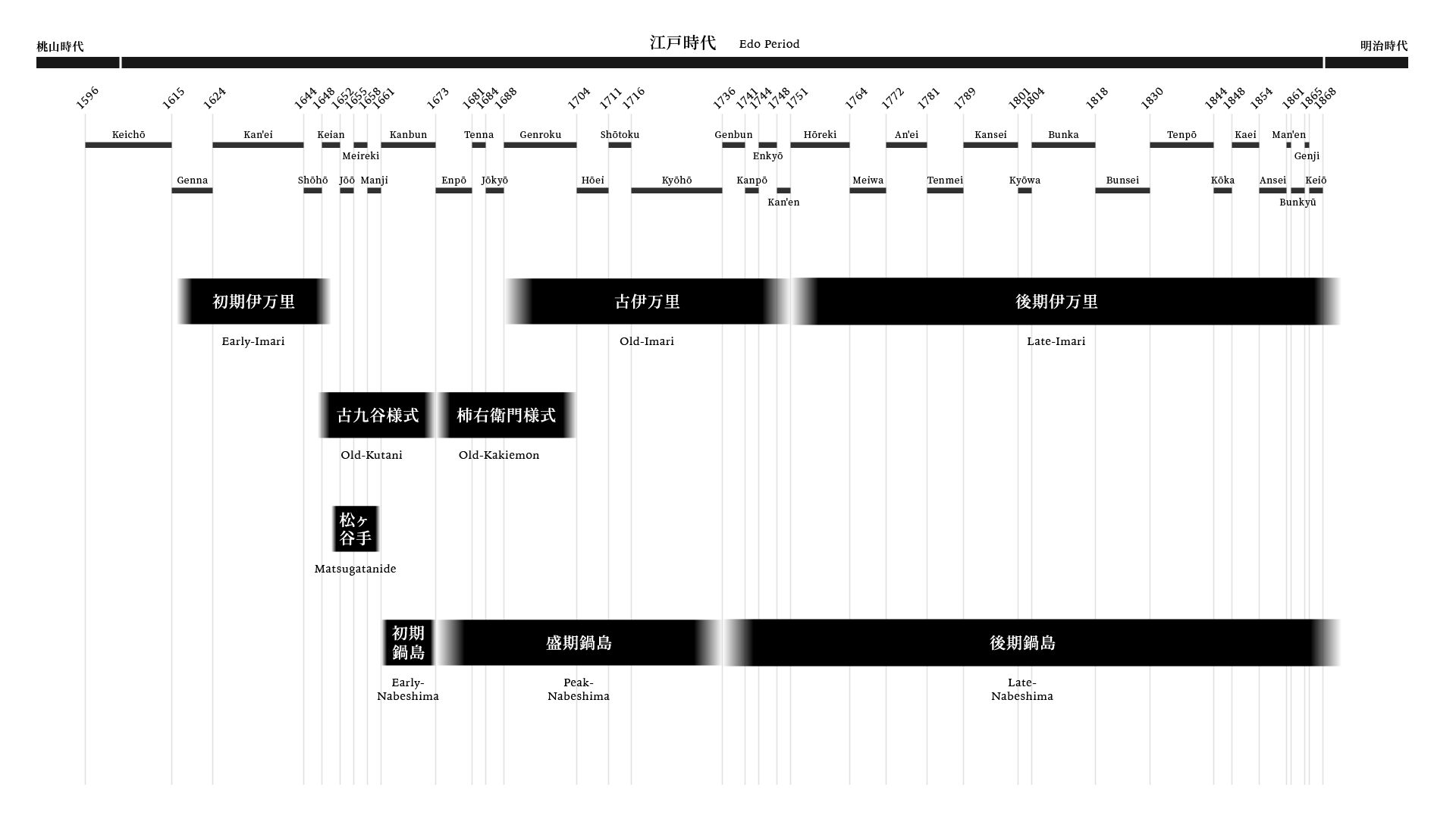
https://tenpyodo.com/en/product1/cat/imari-nabeshima/(Handled Items ⇒ Imari / Nabeshima)
Nabeshima Ware
Nabeshima ware is an exquisite and prestigious specially made porcelain produced at the Nabeshima-domain-kiln in okawachiyama under the patronage of the nabeshima clan of the saga domain in hizen province. This porcelain produced by the nabeshima-domain-kiln, the only imperial-kiln in japan, is a world class masterpiece of porcelain, far superior to old-kakiemon in its technical mastery, and has established an extremely high reputation. It is no exaggeration to say that the highest quality pieces are on par with those produced by the Jingdezhen-imperial-kiln in china. By offering nabeshima ware to the tokugawa shogunate in edo, the nabeshima clan demonstrated its loyalty and obedience. They were also given outside the domain to maintain friendly relations with other feudal lords. Nabeshima ware, unlike imari ware, was not intended for sale but rather as a gift to neighboring regions, so its producers gave no regard to profitability. It is also noteworthy that these kilns did not follow the convention of producing vessels for tea ceremonies, as most clans’ kilns did, but instead focused on practical works, mainly dishes. In the hizen region, pottery production areas were called “Yama”. In the nabeshima domain, the kiln used by the offerings were to fire pottery was called “Odougu-Yama(Nabeshima-Domain-Kiln)”. These kilns were also called “Tome-Yama”, which means the lord’s kiln, to show the utmost respect. In the nabeshima-domain-kiln, the most skillful craftsmen from other kilns in hizen province were called in to establish the nabeshima clan’s unique style of kilns under strict control and in an environment separated from other kilns. According to records from the end of the edo period, 31 potters produced 5,031 pieces per year. These kilns took strict precautions to prevent secret techniques from leaking, such as setting up gates at the entrances and exits and prohibiting the passage of unauthorized visitors. Records tell us that all craftsmen working here were allowed to have family names and carry swords and were exempt from paying any public fees. To reach the site of nabeshima-domain-kiln, which is about 5km north in a straight line from the center of arita town, one has to take a long detour, which is more than 8km long. Such an environment sufficiently isolated the nabeshima-domain-kiln from the outside. Production was modeled after the jingdezhen-kiln in china, with a division of labor by specialty, where each craftsman did his best. Even a single dish went through the hands of many craftsmen. It is said that extra pieces were made in case of breakage during transportation and that 20 pieces were offered at a time. In the peak period, the kilns consolidated the most sophisticated techniques and methods. Blue-and-white, celadon are also well known, but the most famous was “Iro-Nabeshima”. Iro-nabeshima is outlined in paint, glazed with transparent glaze, fired at high temperature(blue-and-white), and overglazed within its frame with the primary colors of red, green, and yellow. This technique was based on the “Tousai” of the chenghua era(1465-87)of china’s ming dynasty. Because these works came from jingdezhen-imperial-kiln, the kilns could create highly sophisticated works without sparing any effort or regard for profit. The designs reflect japanese taste, departing from their chinese and korean influences, and feature unique and sophisticated designs centering on plants from the natural world. These works also draw inspiration from landscape paintings, noh costumes, and momoyama-edo period paintings. A typical vessel of this type is “Mokuhai-Shaped”. It features a high kodai(the bottom part that supports the vessel)made with a potter’s wheel. Kodai are thought to have taller bases than regular works from arita kilns to show their prestige. Many kodai works have a unique design called “Kushiba design(comb teeth design)” around the outer surface painted using blue-and-white. Generally, this technique was only allowed for the nabeshima-domain-kiln at that time and strictly forbidden in other kilns. In the peak period, these works employed a meticulous technique of painting inside the outlines drawn using blue-and-white. However, as time went on, the lines gradually became longer and the brushstrokes more disorganized, and a trend toward simplified, single line outlines gradually emerged. The works underwent several rigorous inspections by officers, and only those that passed were delivered to the clan, while any remaining rejected works were destroyed. The nabeshima-domain-kiln was dismantled in 1871 with the abolition of feudal domains and establishment of prefectures.
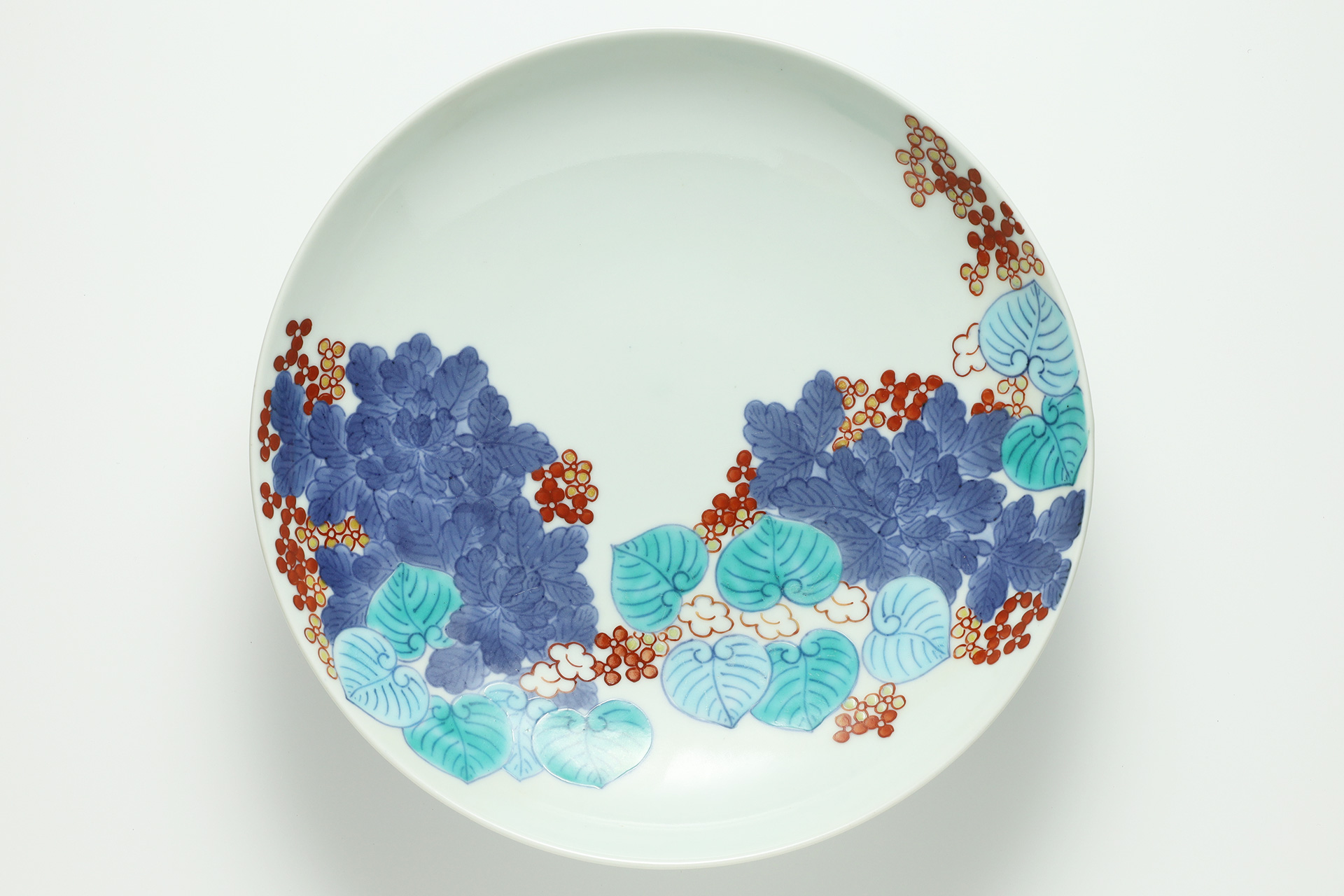
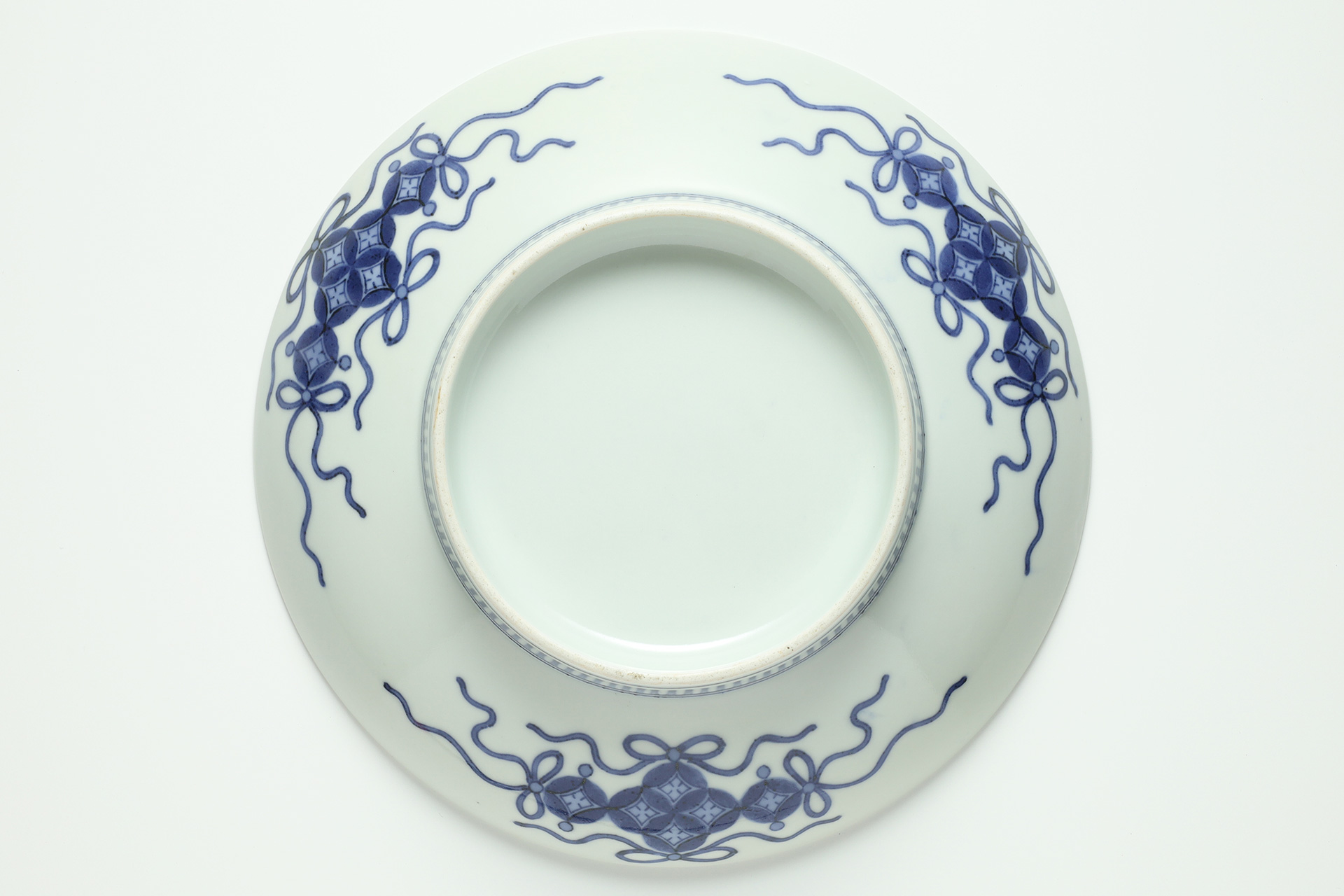
Incipient-Nabeshima of the Iwayagawachi Domain Kiln
Katsushige Nabeshima, the first lord of the saga domain in hizen province, was on the anti-tokugawa(western)side in the battle of sekigahara and offered imported chinese porcelain to the shogunate to restore relations. As a result of the civil war between the ming and qing dynasties in 1644, which made it difficult to import chinese porcelain, there was an urgent need to develop unique porcelain suitable for tribute to the shogunate. It is speculated that the iwayagawachi domain kiln in arita were ordered to accomplish the task. The third shogun, Iemitsu Tokugawa, personally inspected these prototypes in 1651, and as a result, nabeshima ware is thought to have been offered to the shogunate every year. Irregular shaped dishes and cups, classified as “Matsugatanide” can be presumed to be examples of incipient-nabeshima made at the iwayagawachi domain kiln. The design on the reverse side and the inside of the kodai supporting the vessel are left blank and unmarked, and the absence of meato(marks left by stacking vessels for firing)distinguishes this pottery from that of arita’s private kilns. The bottom of the kodai was carefully carved out on three sides, and it took masterful and outstanding skills to create such thin and deeply engraved kodai. Subsequently, flat kodai with less noticeable corners gradually became more common, and the corners were further rounded off as time went on. Saggar, which were unglazed and fire resistant containers, were essential for firing porcelain without meato and without distorting the porcelain. In the 1650s, some of the higher grade works in the sarugawa kiln were unglazed. At this time, the overglaze enamels method was still in its trial and error phase. Because nabeshima ware was intended to be presented to the shogun, it underwent a transition sensitive to changes in the tokugawa shogunate, which was the absolute power in the japanese feudal system. In 1659, the period of full scale trade with the dutch east india company(VOC)began. Around the 1660s, the prestigious domain kiln was separated from odoguyama in arita and moved to okawachiyama(now imari city), surrounded by steep mountains, where they were better hidden from the public. After this arita-nabeshima period, nabeshima ware was fully established at the nabeshima domain kiln in okawachiyama.
Matsugatanide
Matsugatanide differs from old-kutani style and is a group of irregular shaped dishes and cups that share some similarities with early-nabeshima(old-nabeshima)forms and glazes. It was once speculated that “Matsugatani ware” was fired in the ogi domain, a subsidiary of the saga domain, and this theory has been advocated mainly by antique porcelain enthusiasts. However, various research findings have revealed that it is not matsugatani ware. Pottery shards with overglaze enamels base matching the matsugatanide tradition have been excavated from the sarugawa kiln in iwayagawachi and are considered to be the work of the nabeshima domain kiln(okawachiyama), which precedes the domain kiln in iwayagawachi(odougu-yama).
Main Characteristics of the Matsugatanide
- They are bisque firing.
- They have perfect shapes with no distortions.
- There are no inscriptions on the reverse side.
- They are no meato on the inside of the kodai.
- The bottom of the kodai is carved out on three sides to prevent sand from fusing to the bottom.
- Most are irregular shaped dishes with a diameter of about 15.0 cm or small, cylindrical sake cups.
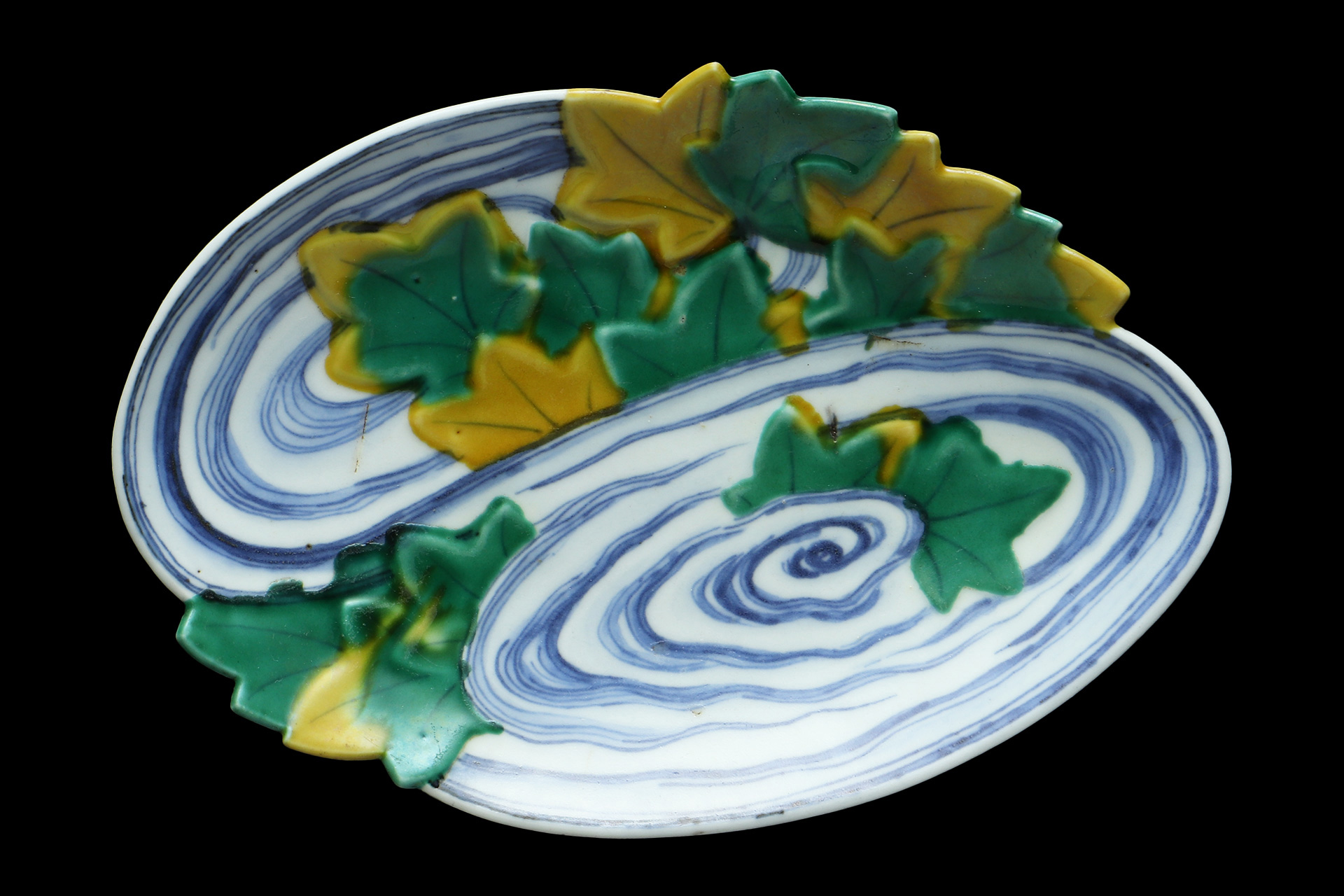
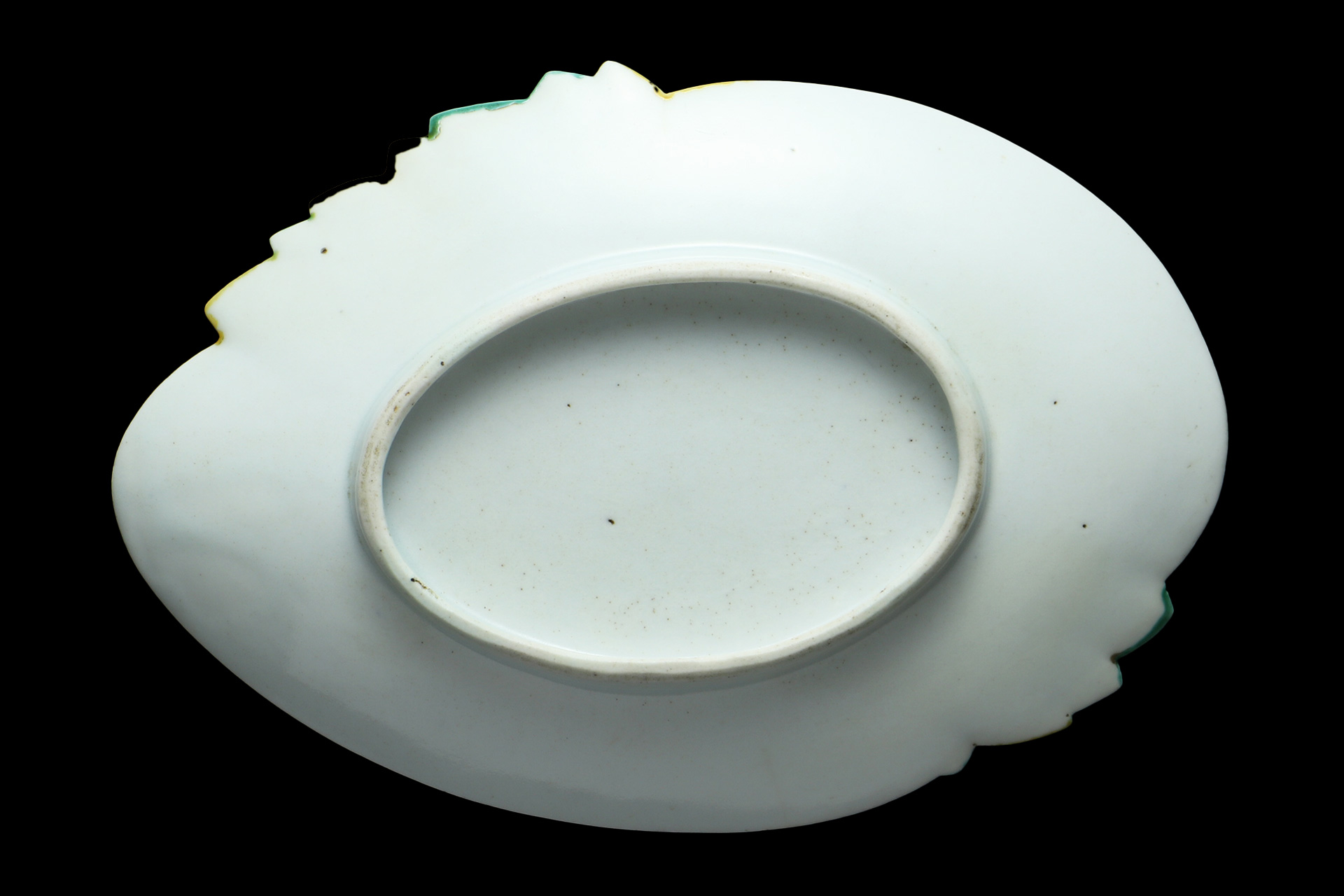
Early-Nabeshima(Old-Nabeshima)
The early-nabeshima(old-nabeshima)was produced in the nabeshima domain kiln in the 1660s. The nipposya-shita kiln(nipposya is a shrine dedicated to Naoshige Nabeshima)was one of the first domain kiln at okawachiyama and produced both products for the general public and exquisite fine porcelain by offering at the same time. Shallow dish with a standardized mokuhai shaped(a high stand supporting the vessel)began to appear at this time. Focusing on small dishes of about 15.0cm and irregular shaped dishes in slightly rich colors, in addition to blue and white porcelain, a technique of outlining with paint and firing at high temperature with a transparent glaze, these works combined overglaze enamels, celadon, cobalt blue glaze and iron glaze techniques. The overglaze enamels technique at this time not only employed blue and white but also underwent much trial and error, such as adding red outlines. The designs on the kodai holding the vessel include yomodasuki design(design with various patterns in a square lattice), hato design(wave design), heart tsunagi design(design with connected heart shapes), kyoshi design(triangular design resembling sawtooth), kaminari tsunagi design(angular spiral design), kensakirenben design (design that looks like the tips of swords lined up), and shippo musubi design. The kushiba design (comb teeth design), which became the mainstream after the peak period, is less common. In the peak period, the standard was often strict, and regulations often bound the work, but at this time, there were many dynamic works with liberal shapes and many small cups.
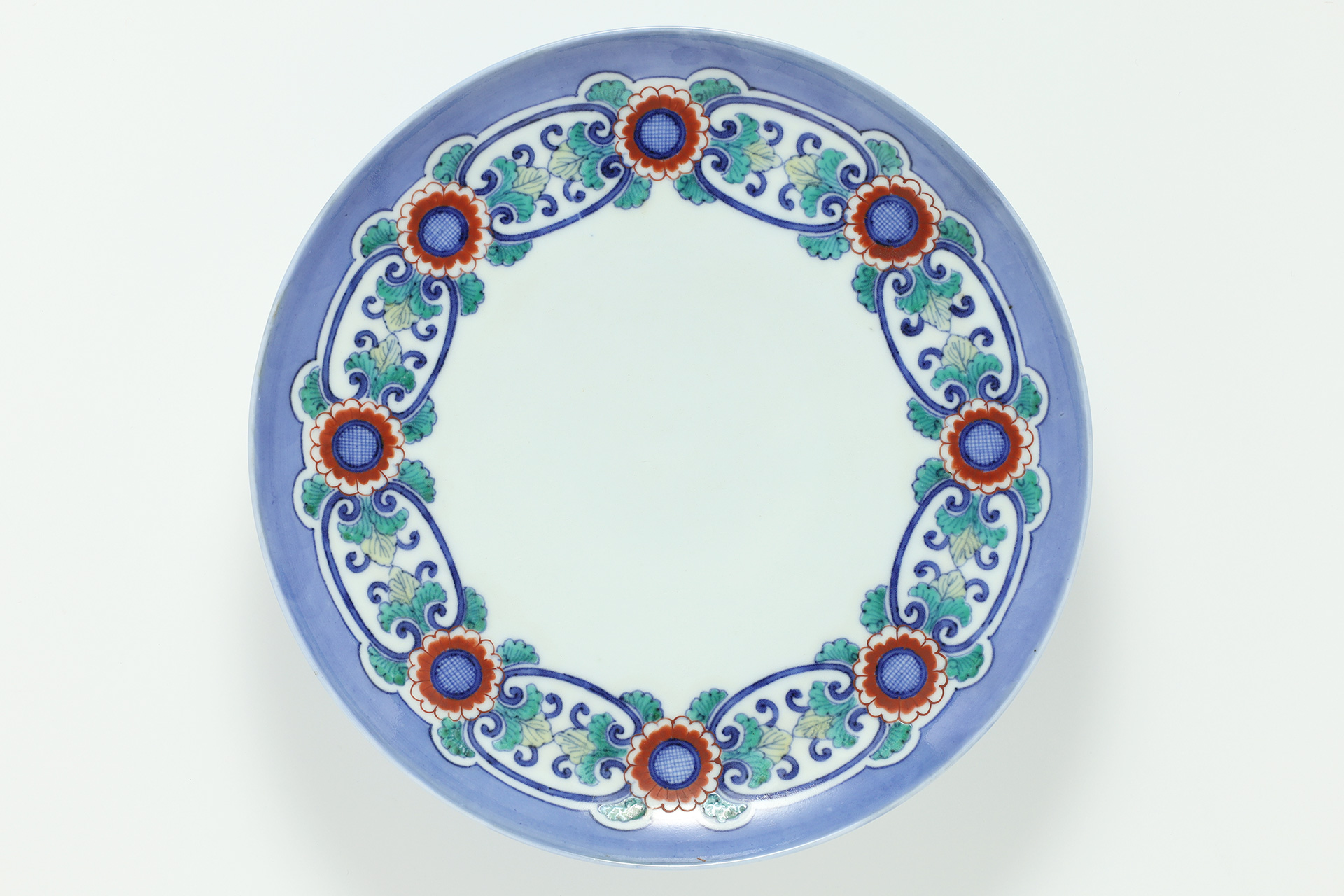
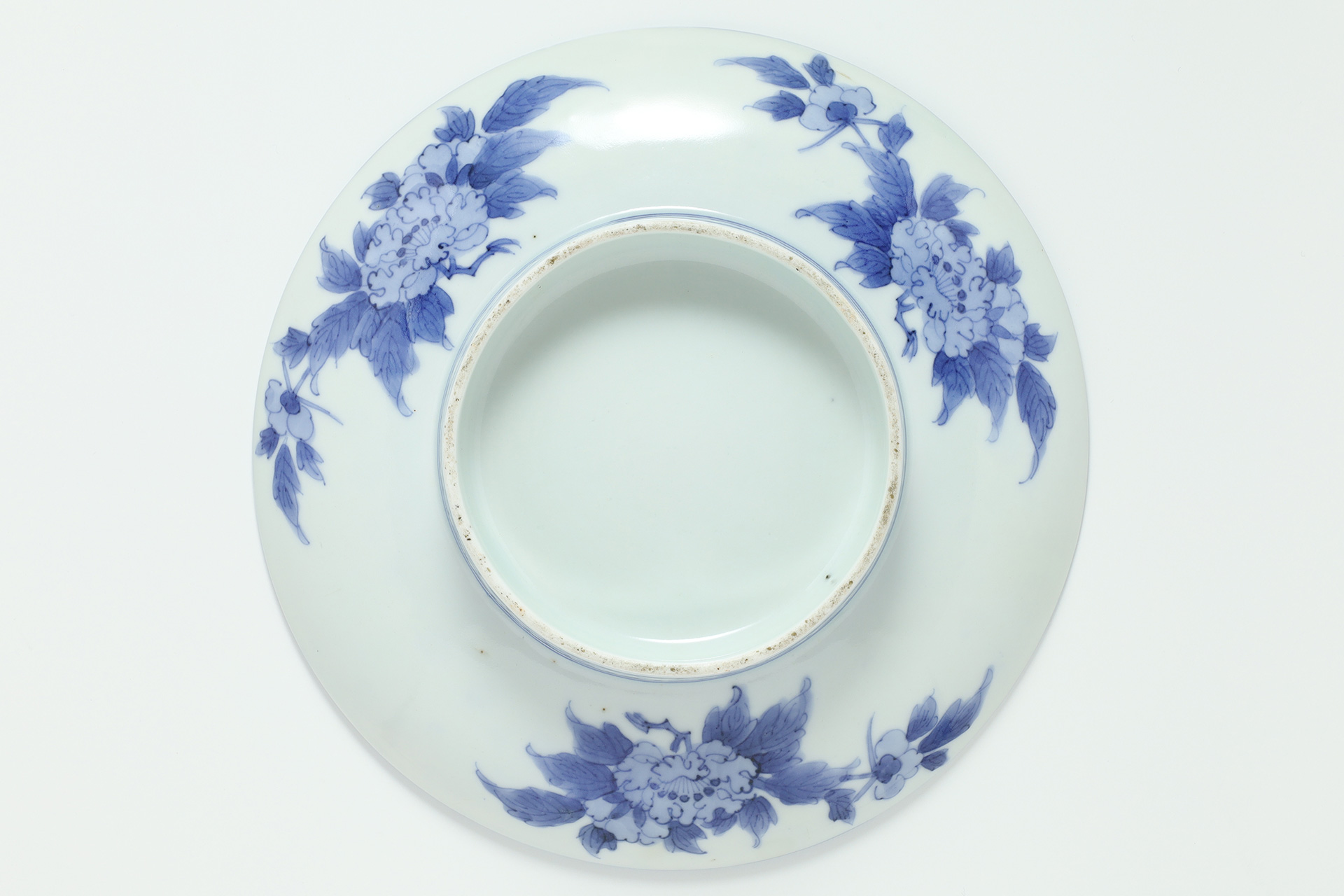
Peak-Nabeshima
The peak-nabeshima was produced in the nabeshima-domain-kiln in the 1670-1730s. According to a letter issued in 1693 by the clan office in the name of 2th Mitsushige Nabeshima to the bureaucrats in charge of arita sarayama, orders were given to maintain strict control of offerings and strictly adhere to delivery deadlines, create innovative and excellent porcelain by incorporating good designs from wakiyama(a private kiln in arita), rather than always using the same method, prohibit craftsmen from entering the wakiyama area to prevent leakage of techniques from clan owned kilns, destroy defective works within the kiln’s premises, bring in any exceptional craftsmen from the wakiyama area, dismiss any poorly performing craftsmen including those who have worked at the kiln for a long time, etc. This order led to a significant change in the style of nabeshima ware. In fact, if we look at the nabeshima ware designs from this period, we can see many that were used for a long time in the privately owned kilns of arita. The technique of painting the kodai, which is the base supporting the vessel, in a manner reminiscent of the comb teeth, was also used in wakiyama in the 1640-1650s in places such as the sarugawa-kiln, etc. It can be said that the technique perfected in the kakiemon-kiln, nangawara, kamanotsuji, etc. Appeared in a refined form in the peak-nabeshima, such as the technique of painting the inside of the outline in a blurred manner. Nabeshima ware, with its primary focus on pictorial designs and the introduction of techniques such as leaving the center blank, achieved unparalleled precision and perfection and was the pinnacle of japanese porcelain. Many of the typical iro-nabeshima are from this period that produced many technically demanding large dishes. The curves of the dish are also well proportioned and superbly balanced. The fact that kodai was more expensive than ordinary arita private kilns was meant to create a sense of prestige, and the design on the reverse side was mostly a combination of vertical lines in the shape of comb teeth and shippo design. Some rare works even gold color.
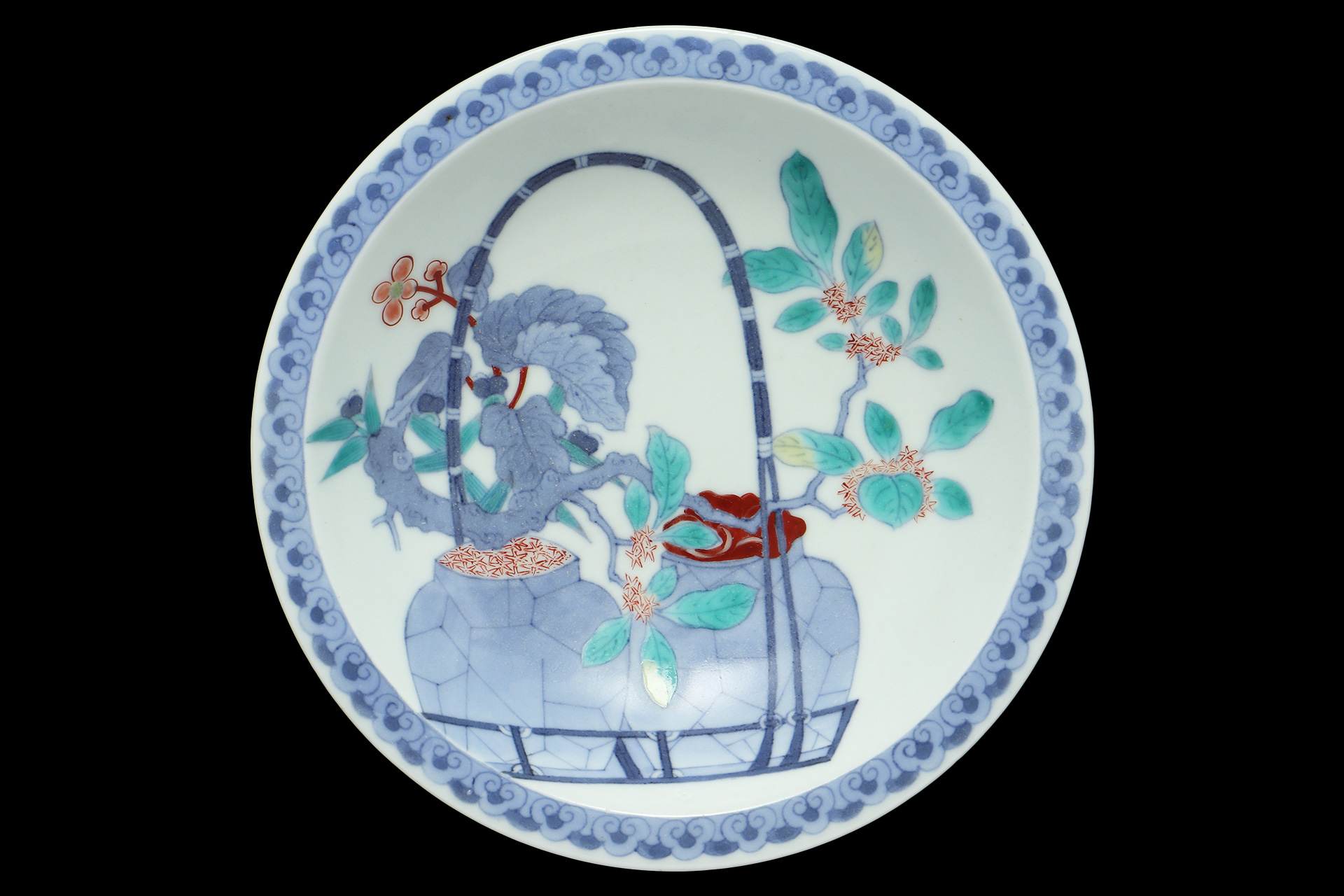
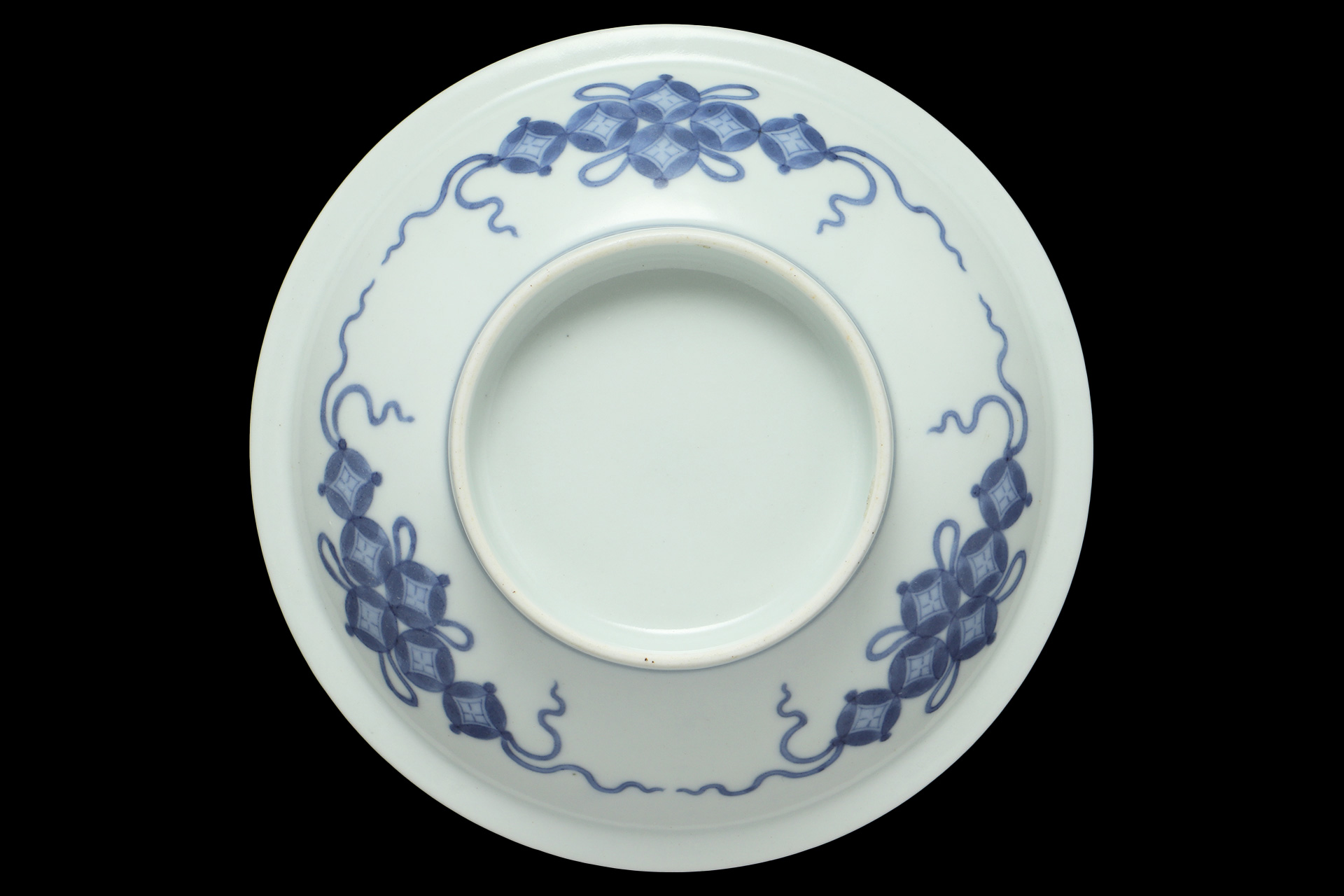
後期鍋島
江戸後期以降の鍋島焼は技術的に精緻さが失われる他、
高台内に紀年在銘や制作者記号を入れた物が現れる等、
制作に当たっての制約にも緩みが生じてきます。
8代将軍・徳川吉宗(1684~1751)は幕府財政の再建を目的として「享保の改革」を行いました。
1722(享保7)年に贅沢品や華美な物を廃す倹約令が出され、
1726(享保11)年に幕府より例年献上陶器に種類の多い色絵具で装飾した物は制限し、
青磁はこれまで通りと命じられました。
こうして最盛期を彩った色数の多い色鍋島は消え、
赤色や二色の色鍋島は例年献上以外で少量のみ焼成されましたが、
染付、次いで青磁が圧倒的な数を占めるようになります。
後期以降の裏文様には牡丹唐草(蟹牡丹)文が圧倒的に増加し、
櫛高台に七宝結文の組み合わせは、
牡丹唐草文の裏文様よりも相対的に粗放な作行の物が多く、
例年献上以外の贈答や藩用品として造られた可能性が強いように考えられます。
寛政年間(1789~1801)頃からは町人層へも広く鍋島焼は流通していたと考えられています。
江戸後期以降の全国諸藩の財政は極度に悪化していたと考えられており、
藩より富豪商人への借銀返済の一端として使用されたと思われる例も確認されています。
鍋島藩から直接的に町人層へ渡っていたとは考え難いのですが、
富豪商人を経て、最終的に経済的優位な状況にあった町人層へも流通したと考えられます。
鍋島藩は幕末に外国船が来航する長崎での防備の経済的負担が大きくなった為、
幕府に願い出る事で初めて、
1857(安政4)年に例年献上を5年間免除されました。
将軍家御好みの意匠・十二通り
各大名家から徳川家へは「月次献上」として毎月様々な品物が納められていました。
鍋島焼は11月の献上品であり、
1770(明和7)年には鉢2枚、大皿20枚、中皿20枚、小皿20枚、
茶碗と皿と猪口の内20個をセットとして5箱分が献上されたという記録が残されています。
20枚1組となる皿類は組食器として同文様で構成されていました。
この月次献上に合わせ、多くの幕府高官、佐賀藩と縁のある諸役人、親戚等へも贈答された為、
相当な点数が造られた事が窺えますが、
現在では散逸して、組食器としての本来の姿を偲ぶことができる例は貴重です。
10代将軍・徳川家治時代の1774(安永3)年に佐賀藩は献上陶器についての指示を受け、
以後の将軍家献上の鍋島スタイルが確立されます。
詳細は「例年献上の陶器五品の中に十二通りの品から二・三品を含めるように」という事でした。
この「将軍家御好みの意匠・十二通り」に該当する作品は、
梅絵大肴鉢、牡丹絵中肴鉢、菊絵大角皿、山水絵中角皿、山水絵長皿、遠山霞絵長皿、
折桜絵長皿、金魚絵船形皿、萩絵丸中皿、葡萄絵菊皿、蔦絵木瓜形皿、松千鳥絵猪口です。
Nabeshima-Celadon
In japan, celadon (Karamono), which came from the continent, had been highly prized since the kamakura period, and the nabeshima ware had put particular emphasis on celadon. It is also known that the clan moved its kiln to okawachi-yama(nabeshima-domain-kiln) because of the availability of high quality celadon ore. The nabeshima clan thus produced some of japan’s finest celadons, which made a clear impression. Outstanding works bear a celadon color reminiscent of kinuta-celadon, the highest quality celadon produced in china. Nabeshima-celdon was designed to match the quality of the chinese kinuta-celdon and jiaotanxia-imperial-kiln celadon. The glaze consisted of natural celadon ore from okawachi-yama nihonyanagi mixed with the ashes from burning the best japanese cypress, which produced the soft, beautiful porcelain surface made during the peak-nabeshima. Although this celadon produced a deep color by applying multiple layers of the glaze, it had to be fired in a kiln each time, which entailed the risk of defects. Because the clan undertook the production of nabeshima ware, meant to be presented to the shogun and other feudal lords, it was possible to take such risks without regard to profit when firing celadon. While most common celadons only feature celadon-glaze, nabeshima-celadon uses the blue-and-white(sometsuke) technique(a technique of painting designs, applying a transparent glaze, and firing at a high temperature) and overglaze enamels. The celadon blue-and-white(sometsuke) for nabeshima using celadon-glaze containing gosu(a blue dye used for porcelain) has celadon-glaze applied at least twice, then gosu, along with another coating of celadon-glaze before firing. In this way, the works undergo a meticulous production process in which they are fired at least three times.
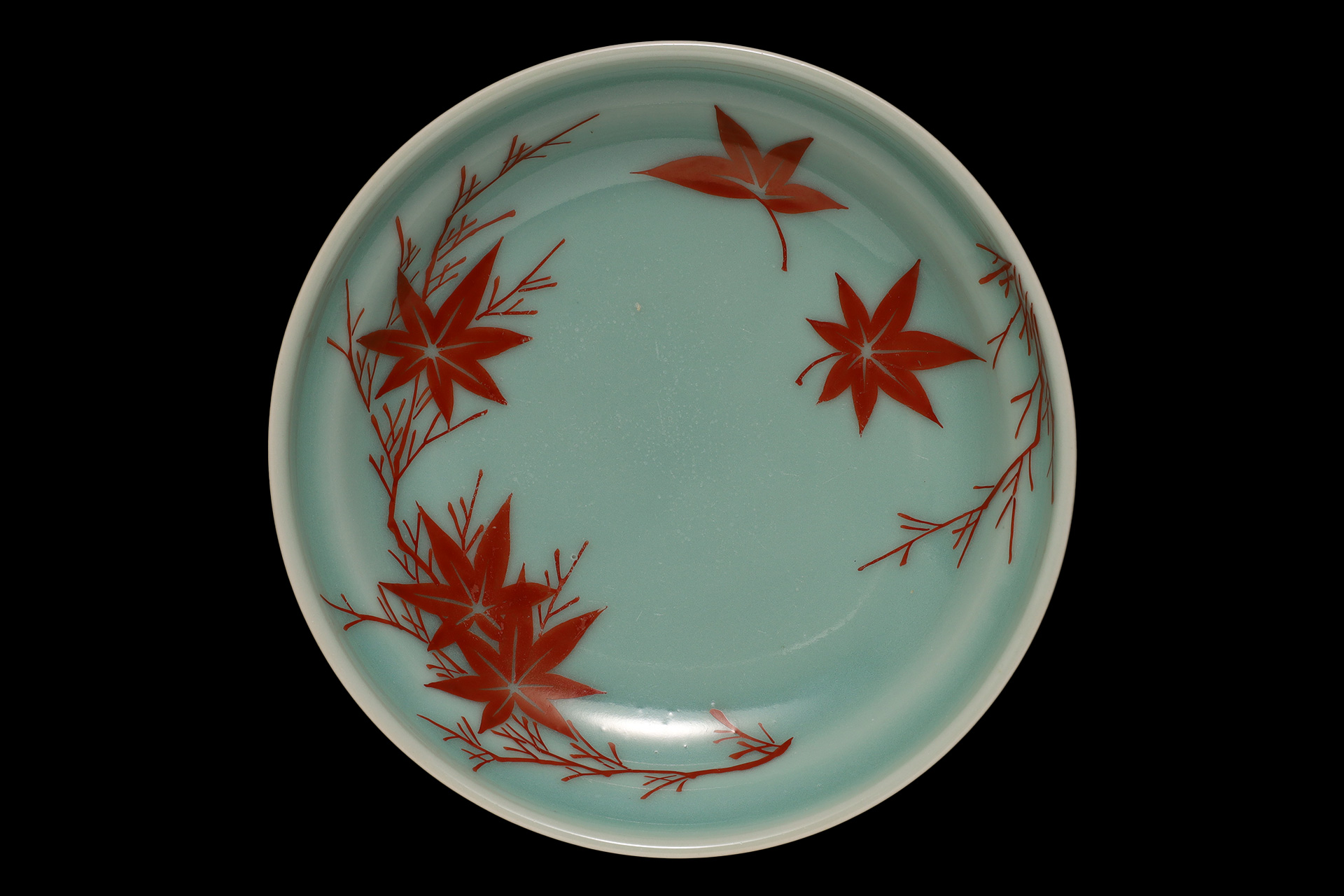
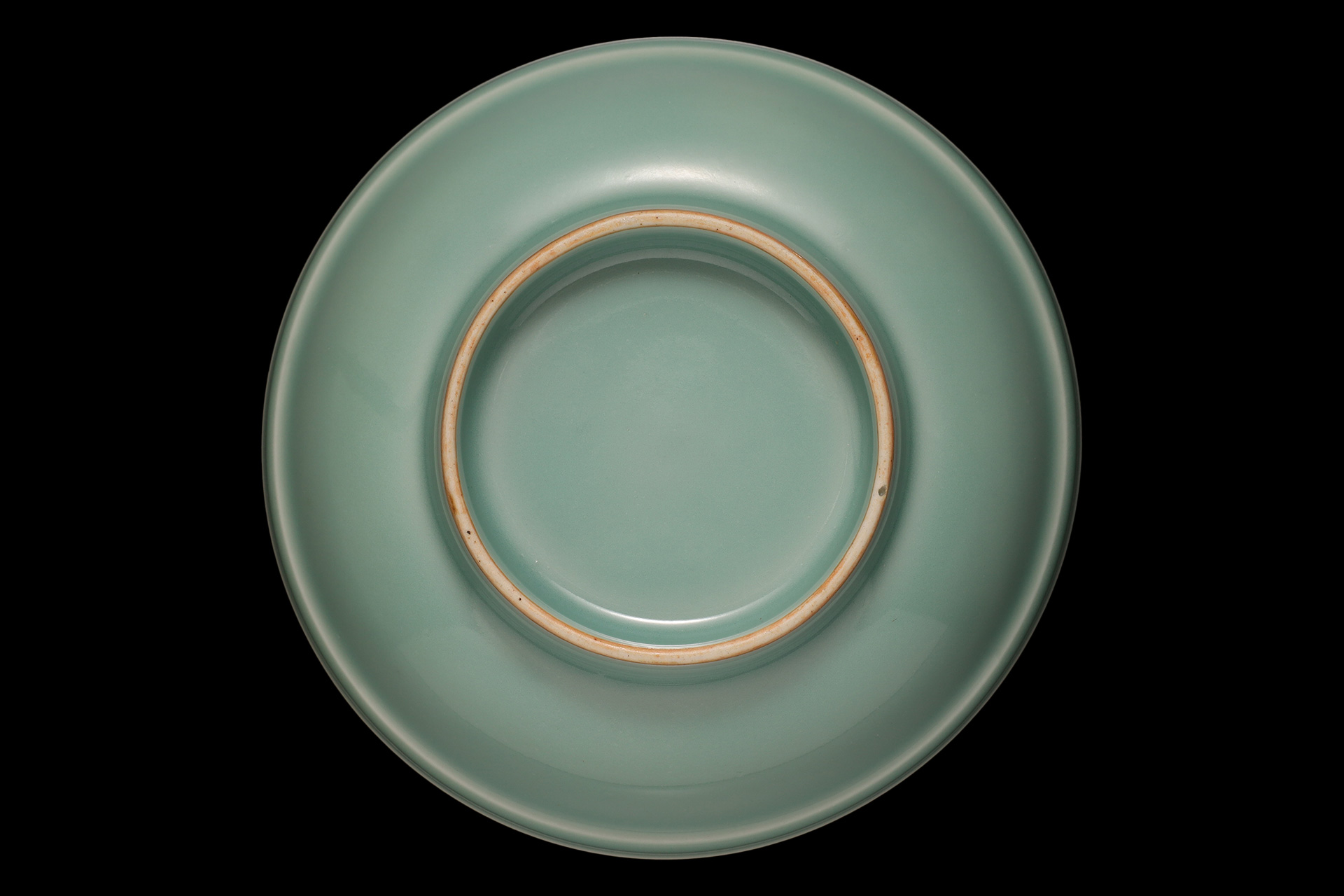
We sell and purchase Nabeshima Ware
We have a physical shop in Hakata-ku, Fukuoka City, where we sell and purchase "Nabeshima Ware" works. Drawing on a long career and rich experience in dealing, we promise to provide the finest service in the best interests of our customers. With the main goal of pleasing our customers, we will serve you with the utmost sincerity and responsibility until we close the deal.