Old-Kutani
古九谷様式
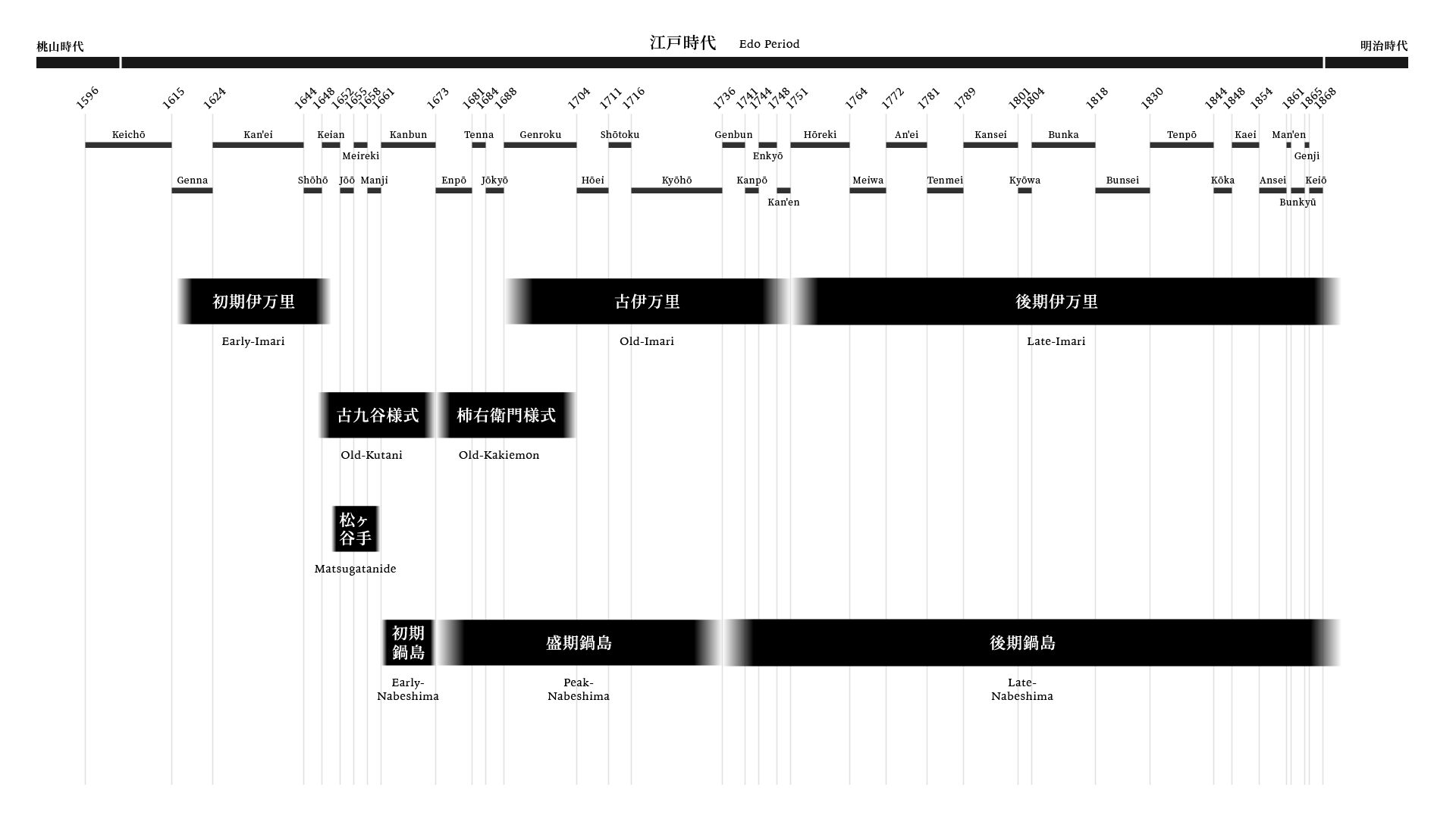
https://tenpyodo.com/en/product1/cat/imari-nabeshima/(Handled Items ⇒ Imari / Nabeshima)
Old-Kutani
Old-kutani is a style of imari ware developed in arita, hizen(current saga prefecture), in the early edo period. In the 1640s and 50s, the overglaze enamels technique was introduced to imari ware, which before then was primarily blue and white pottery. Thanks to this dramatic change in technique, early-imari was developed into “Old-Kutani”. Overglaze enamels porcelain, which was originally created by imitating chinese ceramics, developed independently in japan, and in addition to the bright dishes designed for dinner parties, there were also a lot of works created for tea ceremonies and kaiseki. Some pieces were made with noticeably higher quality color painting technique, and it is thought that artists of painting may have contributed to making these pieces. The number of works with inscribed name grew dramatically, and a wide variety of inscribed names were used, such as “Kakufuku” or “Homare”. Since the dishes being made had become wider, in order to prevent the middle of the dishes from sagging during firing, a technique was developed that involved adding cone shaped supports made out of the same material as porcelain called “Hari”. Early-imari dishes had smaller bases, so there are very few pieces that show signs of the use of these “Hari,” other than large dishes. Iroe(overglaze enamels)old-kutani have a magnificent, powerful character, and due to their unique design style and thick, oil paint like coloring, for a long time it was commonly believed that they were produced in kaga(current ishikawa prefecture)- this is known as the kaga theory – but after several pieces of overglaze enamel pottery in the old-kutani style were found in the remains of old kilns in arita, the hizen theory, which claims that they were fired in arita, hizen(saga prefecture), became more prevalent, and this is the mainstream view today. Thanks to the strenuous efforts of hizen potters in the middle 17th century, these beautiful vessels still exist today, and rival jingdezhen porcelain, which is said to be the highest quality porcelain in the world.

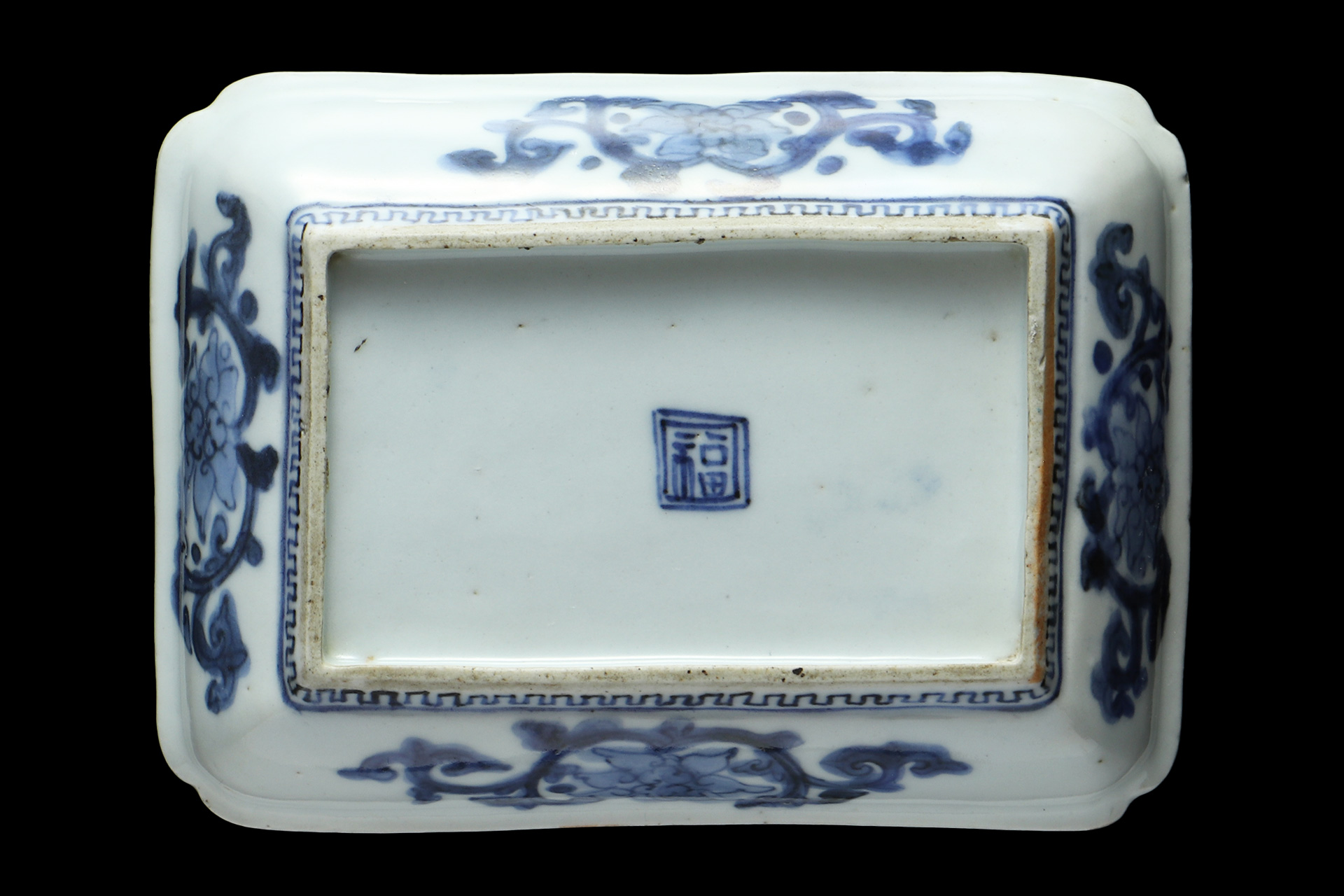
Old-Kutani Debate
- Created in kutani, kaga(ishikawa prefecture)→ Kaga theory
- Created in arita, hizen (saga prefecture)→ Hizen theory
In 1914, Seiichi Okuda and his group, which was centered around Masatoshi Okouchi(1878-1952), founded the ceramics research society at the psychology class of tokyo imperial university. The research society “Saikokai” was born from this group, and they aimed to perform scientific / academic research unconstrained by old ways of thinking. Mr. Okouchi had a significant impact on how old pottery was perceived as well as old-kutani research, and laid the foundations for modern pottery research, but in 1938, Daisuke Kitahara proposed the hizen theory, claiming that old-kutani was created in arita, hizen(saga prefecture), and after Mr. Okouchi’s death, this theory spread further and further. A group of researchers including Sakuro Yamashita visited the sites of old kilns in arita to investigate themselves, and in 1968 they published “Old-Imari and Old-Kutani,” advocating for the hizen theory. From 1972-1975, an examination of the remains of the yanbeta kiln was conducted, and a lot of unglazed pottery bearing the five colors characteristic of old-kutani, as well as blue and white patterns on the inside, was found, along with fragments of pottery with overglaze enamels. A lot of overglaze enamels were also found at kilns such as kusunokidani, maruo, tataranomoto, sarugawa, chokichidani providing concrete evidence for the hizen theory. Furthermore, in 1988, the ruins of akaemachi in arita were uncovered, and aode-kutani and iroe(overglaze enamels)old-kutani pieces were found there. Overglaze enamels have also been unearthed in kaga(ishikawa prefecture), but it has been pointed out that many of these are shaped differently to pieces in the old-kutani style. In recent years, it has become possible to measure trace elements found in pottery flakes and clay, and fragments of overglaze enamels old-kutani were analyzed, which showed that they bear a close resemblance to pottery produced in arita.
Introduction of Overglaze Enamel Techniques
In hizen during the edo period, overglaze enamels were known as “Akae”. In the 1640s, due to the influence of chinese pottery, a type of old-kutani called overglaze enamels porcelain emerged. Unglazed pottery with overglaze enamel is fired at approximately 1300℃, after which a pattern is painted on with colors like red, green, yellow, blue, and purple, and it is then put in a nishiki kiln, which is made with two layers to prevent the fire from touching the pottery directly, and fired at a low temperature of around 800℃. Fragments of overglaze enamel pottery have also been found at the remains of kilns such as kusunokidani, maruo, tataranomoto, sarugawa, chokichidani, and it is thought that before saga domain established the akaemachi area to restrict the use of overglaze, potters were using overglaze relatively freely. One factor thought to be a reason not many overglaze enamel fragments have been found is that overglaze pottery is fired at a low temperature, so failure is rare. The nishiki kilns used at the time were small kilns, different to the climbing kilns(Noborigama)used for glaze firing, and were built on flat ground. The unearthing of old kilns is mainly done for climbing kilns built on hillsides, and digs on flat ground aren’t often conducted, with the exception of akaemachi ruins, which is another reason few overglaze enamel pieces have been found. At the time, overglaze enamels porcelain was the most valuable, high class type of porcelain, so it was perhaps inevitable that the people advancing porcelain production would decide to import the overglaze enamels technique.
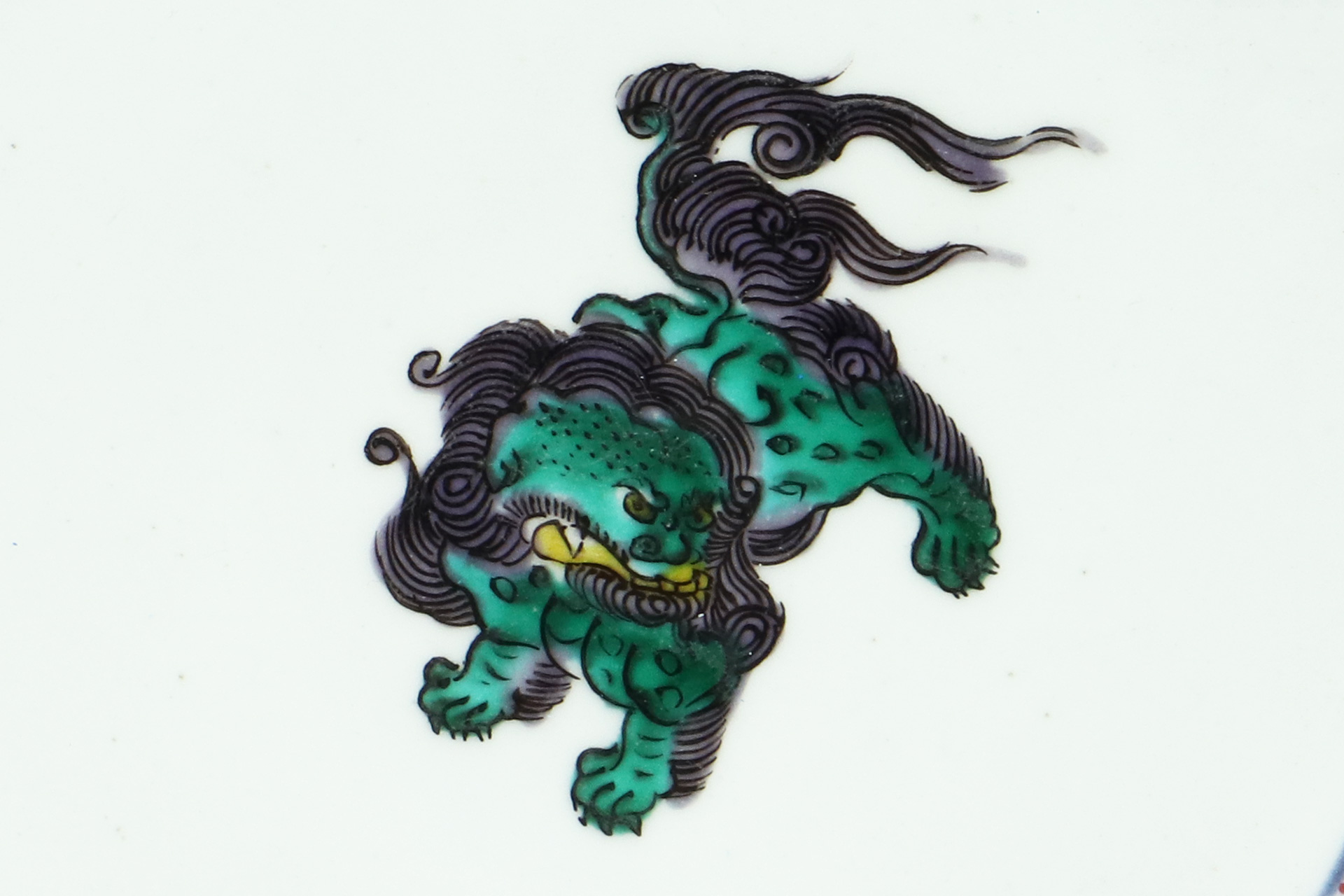
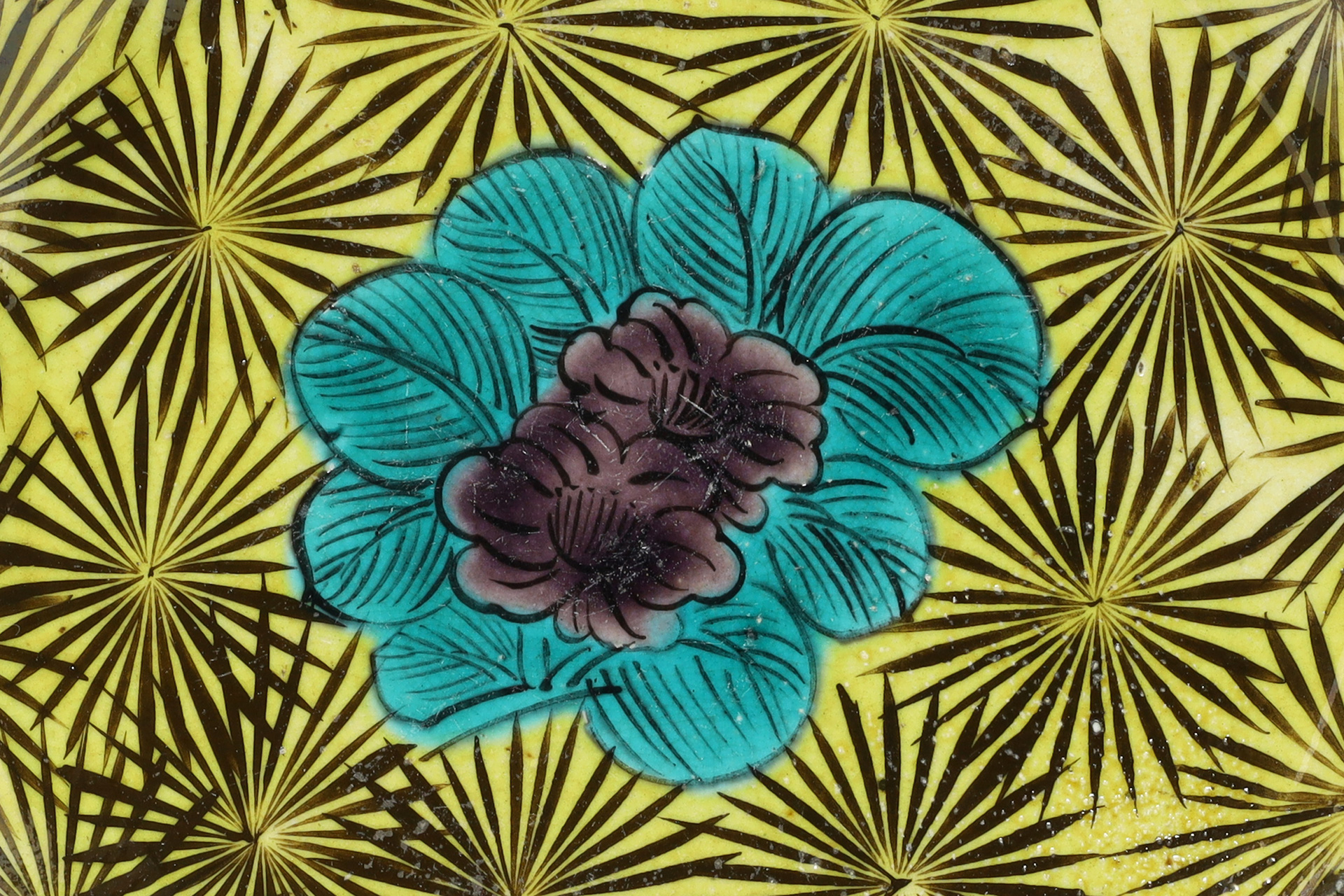
Akaemachi
In 1637, the saga domain government claimed that potters were cutting down too many trees on the mountains for firewood, so they expelled 826 potters, and created 13 kiln areas in the eastern region of arita(this area would later become known as uchiyama, and would be a hub of pottery production). Once the production of overglaze enamels porcelain, which has high value added, became popular, saga domain introduced division of labor into overglaze production, and in 1672, in order to prevent sloppy production driven by competing for profit, as well as the leaking of the akae technique to other domains, the government certified 180 kilns and 11 akaeya(overglaze specialist)businesses, and established akaemachi in the center of the uchiyama region. All unglazed overglaze enamel pottery was systematically transported to akaemachi, where overglaze was applied. To keep the technique a secret, only the eldest son of an akae craftsman could succeed him, and the industry was strictly regulated under the watchful eye of the pottery region’s daikan(local governor). The large bell at houon-ji temple in hiekoba, which existed until wwii, was most likely created in the Kanbun era(1661-1673), and the word “Akaemachi” was written on it, which proves that akaemachi existed at that point in time. Saga domain was trying to build a pottery industry that would financially benefit the domain. By concentrating resources like knowledge and materials in uchiyama, the center of production, they attempted to create an efficient system that would provide reliable profit. The various elements comprising this system were also adopted and discarded over time, with the ones matching the demands of the time being bolstered, while those that didn’t match were thrown out. By the middle 17th century, many important kilns outside uchiyama, such as the yanbeta and maruo kilns, were abandoned. It is thought that many of the overglaze enamel specialists from these kilns were involved in the establishment of akaemachi. When akaemachi was founded, the main market for overglaze enamel was the international market, and to match the tastes of these foreign buyers, uchiyama craftsmen used milky white porcelain to create thin vessels, and mass produced refined, brightly colored overglaze pottery. In 1988, the arita education committee conducted an excavation of the remains of an overglaze enamel pottery creator’s house in former akaemachi(kitajima family), and uncovered ruins thought to be an akaeya kiln, as well as a multitude of overglaze enamel pottery fragments. This material is incredibly valuable for tracing the history of hizen overglaze enamel from the time akaemachi was founded to the present day. The excavation site is called the akaemachi ruins, and fragments of overglaze enamels porcelain like aode and gosaide have also reportedly been found there. It is thought that iroe(overglaze enamels)old-kutani may also have been created at akaemachi, but these pieces were created at the end of the old-Kutani period, so there aren’t many of them. In addition, clay models(including shapes like humans and elephants)in the kakiemon style have also been uncovered, which shows that they were also involved in the creation of these models.
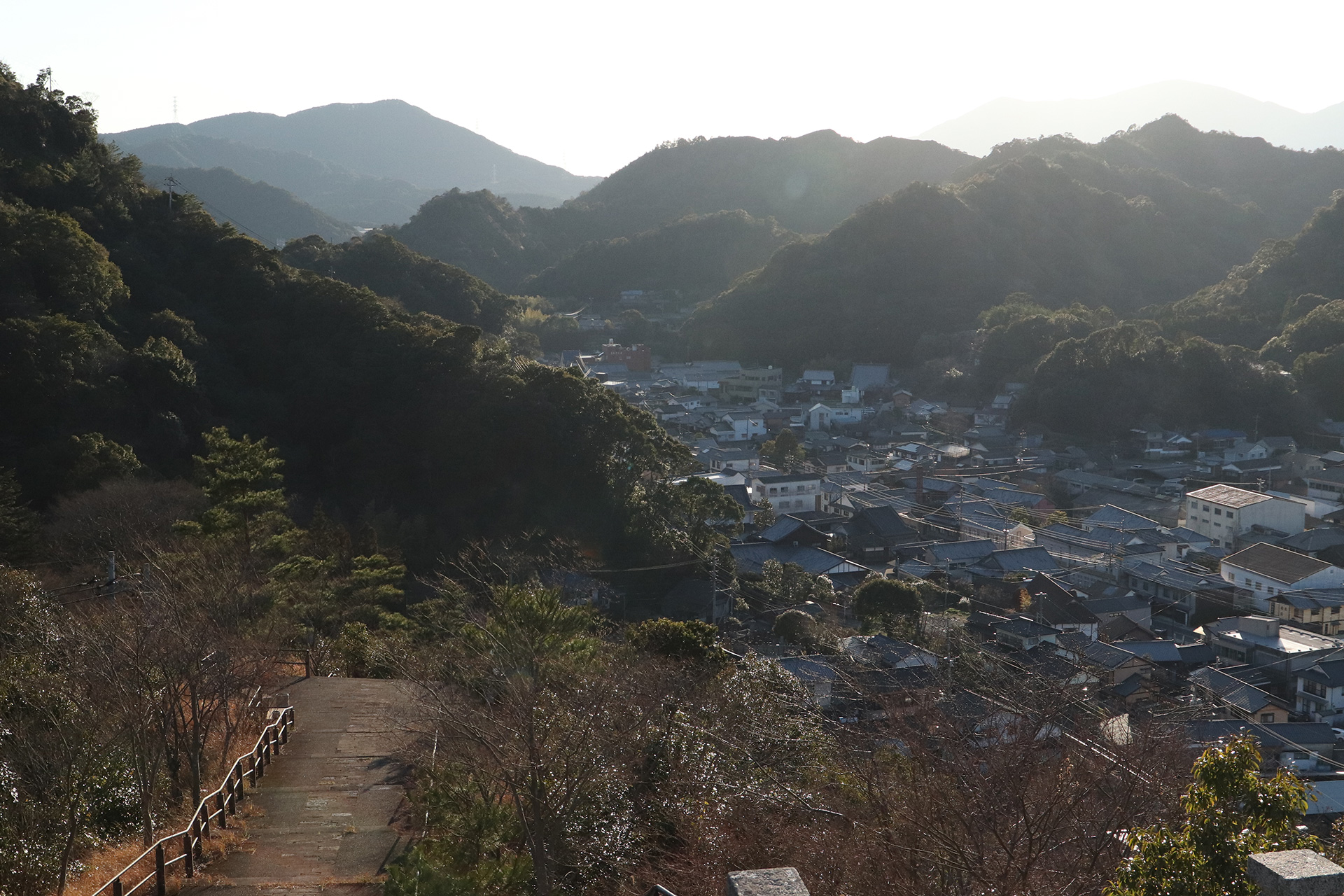
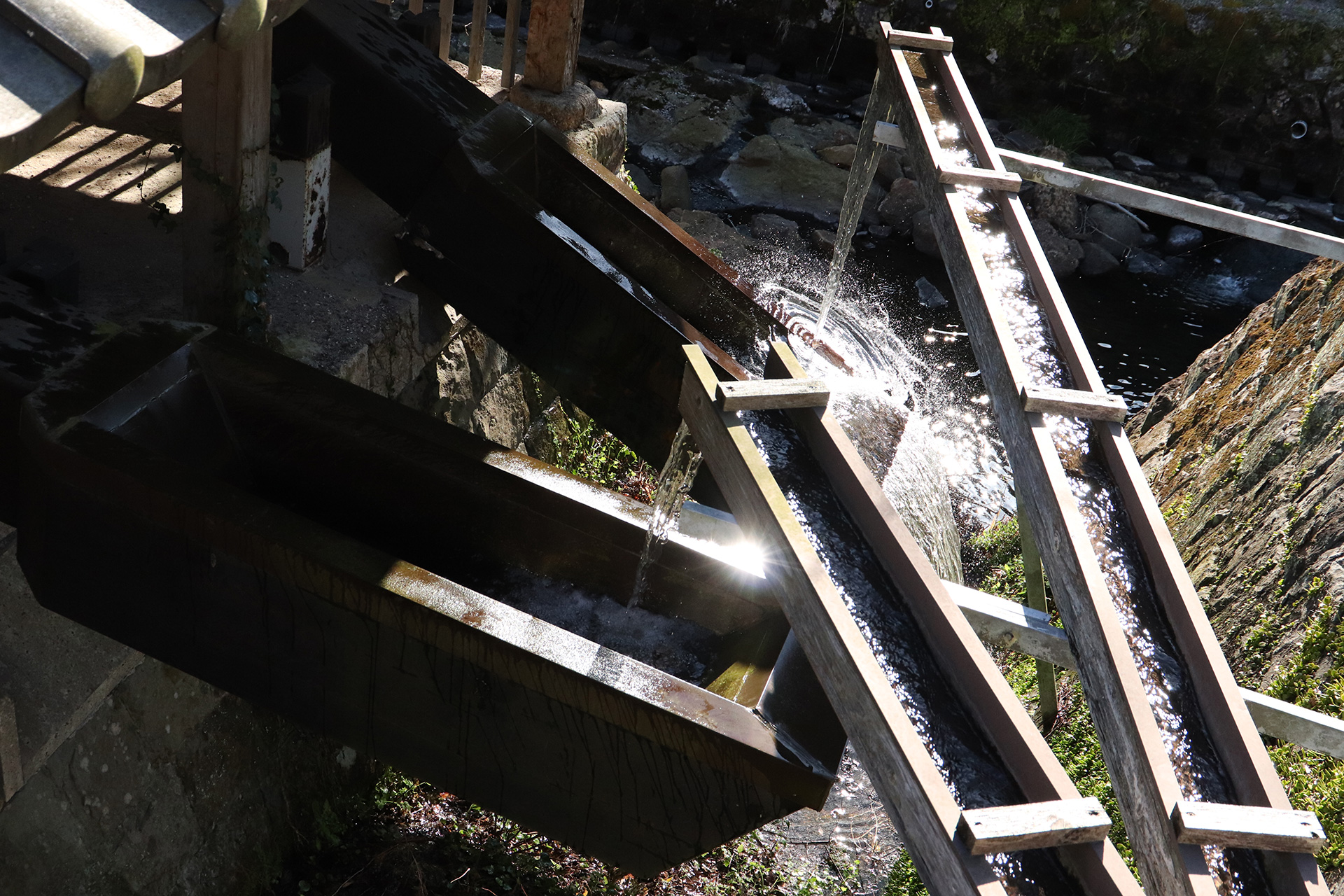
Akae Related Events
- 1637(Kanei 14):The saga domain government claimed that potters were cutting down too many trees on the mountains for firewood, so they expelled 826 potters, and created 13 kiln areas in the eastern region of arita(this area would later become known as uchiyama, and would be a hub of pottery production).
- 1647(Shoho 4):Slightly before this year, the group led by Kakiemon Sakaida invented the akae style(there are various theories surrounding this). Kakiemon brought the successfully created akae to nagasaki, and sold it for the first time to the buyer from the maeda clan of kaga domain(there are various theories surrounding this).
- 1672(Kanbun 12):Saga domain certified 180 kilns and 11 akaeya(overglaze specialist)businesses, and established akaemachi in the center of the uchiyama region. The large bell at houon-ji temple in hiekoba, which existed until wwii, was most likely created in the Kanbun era(1661-1673), and the word “Akaemachi” was written on it.
- 1770(Meiwa 7):The number of registered akaeya businesses was increased from 11 to 16, and the government announced that it would forever be capped at this number.
- 1809(Bunka 6):The number of registered kilns was increased from 180 to 220.
The Maeda Clan and Old-Kutani
It is easy to work out that the production of styles like iroe old-kutani and aode-kutani, which used a lot of expensive overglaze enamel pigments, was an order of magnitude more costly than blue and white pottery. It was therefore mainly sold to daimyo(japanese feudal lord)clans like the maeda clan of kaga domain, and rich merchants in the kansai region. The maeda clan in particular is known for their fondness for chinese ceramics(Kosometsuke, Shonzui, Nanjing-Akae, etc.). Due to the civil disorder caused by the transition from the ming to qing dynasty in the 1640s, exports of jingdezhen porcelain had to be halted, and soon many japanese people were calling for domestically produced high quality overglaze enamel pottery to replace it. Many high quality old-kutani pieces, mainly gosaide, have been discovered at the remains of the maeda clan’s estate(located within the grounds of tokyo university), it has also been pointed out that the nabeshima clan and the maeda clan had a deep relationship with each other. We now know that many old-kutani dishes over 40cm wide(which is quite rare in japan)were created because the japanese aristocracy liked to have large dishes to pile fish and poultry meat onto at their banquets. Since it was one of the status symbols, there are almost no similar works in old-kutani large dish.
Aode-Kutani
Aode is one of old-kutani style overglaze enamels porcelains. This technique of applying glaze at a low firing temperature is speculated to have been influenced by potteries such as cochin ware, underglaze yellow and overglaze green(jingdezhen kiln), which reached their peak in china during the ming and early qing dynasties. The base is mostly single fire glazing without bisque firing. Their qualities vary considerably, from pottery with high quality white porcelain bases, to those with both porcelain and ceramic elements, to those with inferior ceramic bases. The yanbeta kiln is considered the leading production area.
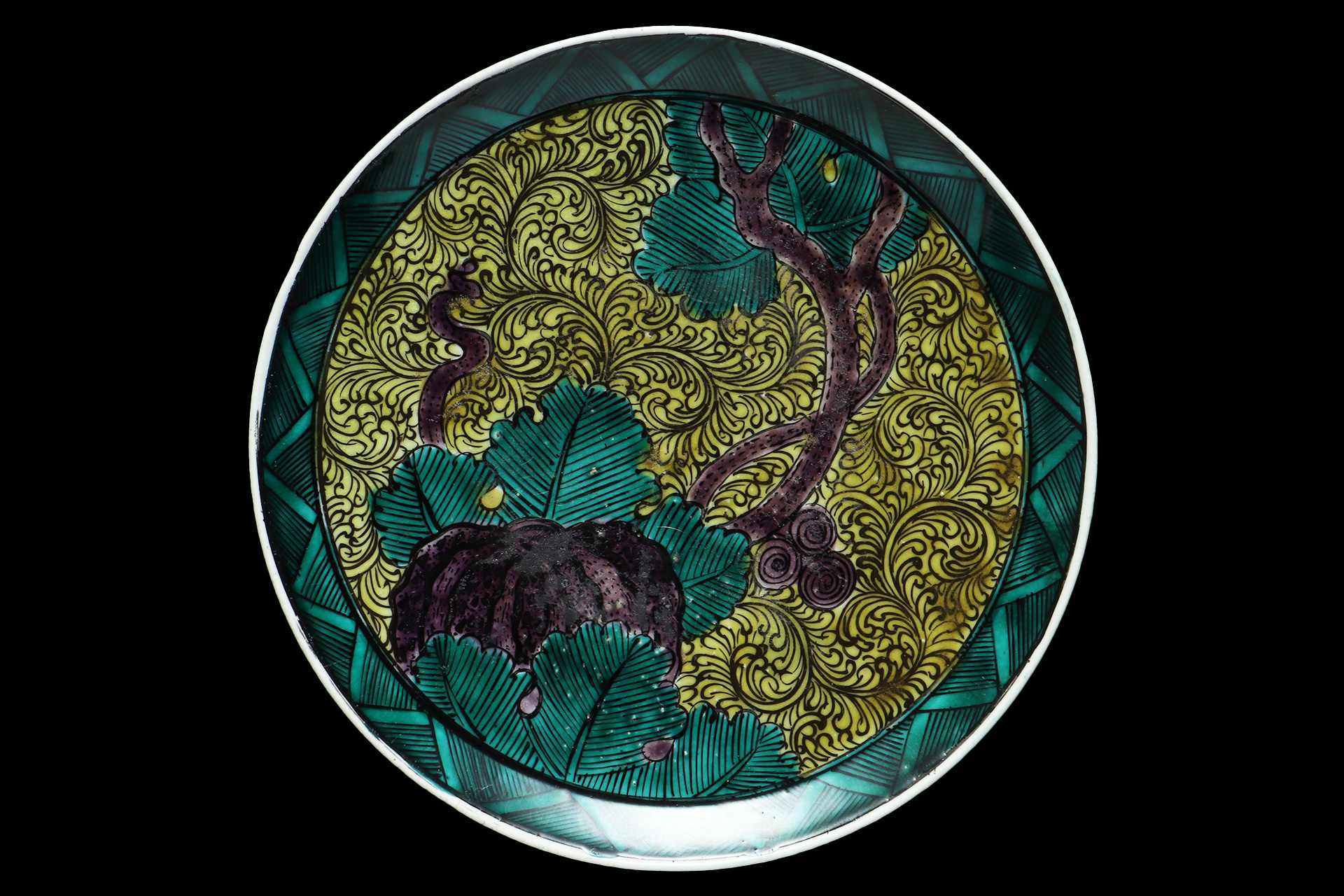
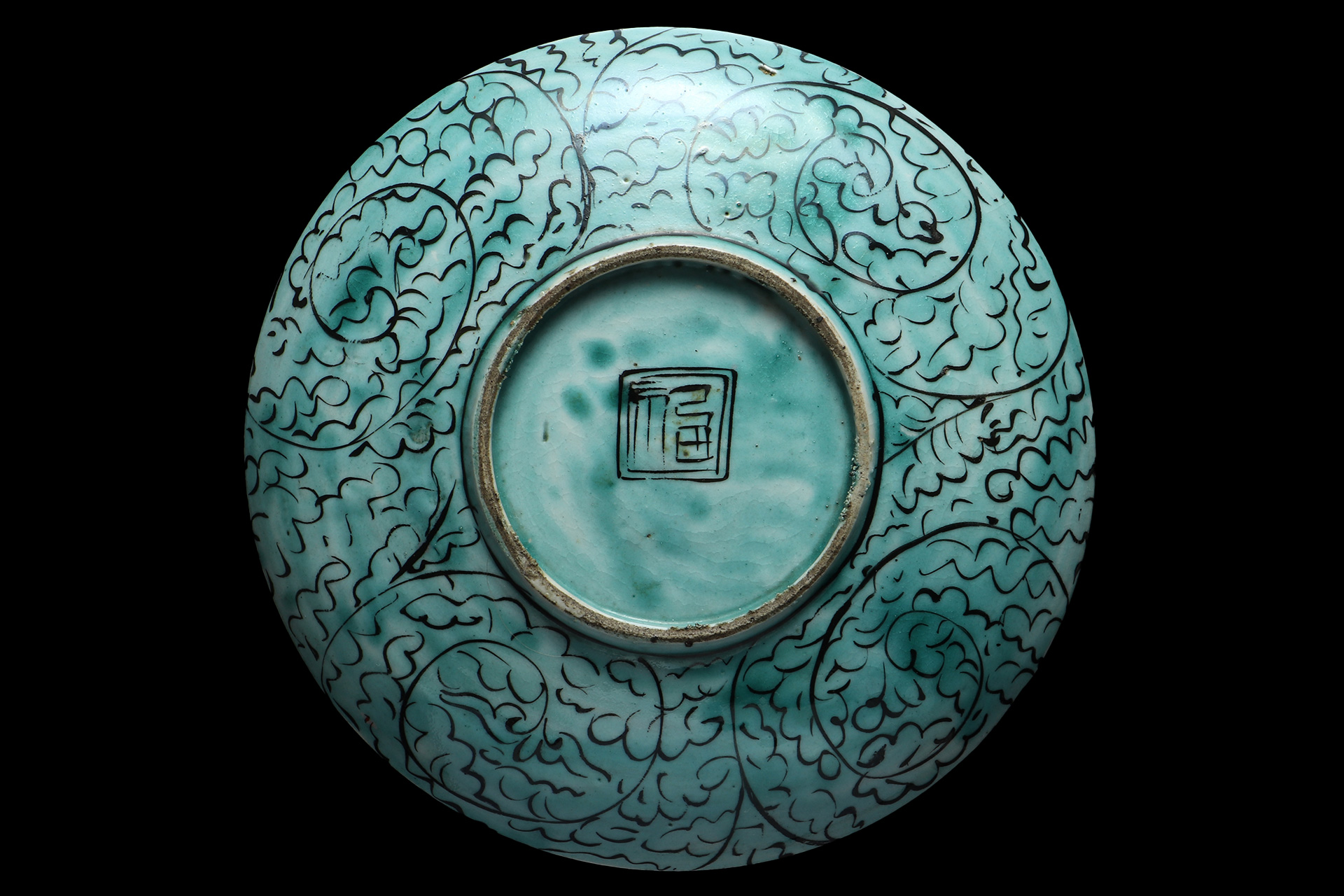
Suisakade
Iron glaze varies in color depending on the iron content in the ceramic glaze, and its classifications are caramel glaze, persimmon glaze, iron glaze, rust glaze, black glaze etc, depending on the coloration. Celadon develops a blue color from trace amounts of iron. Iron glaze works, with their soft appearance, come from a superb technique of single fire glazing. These works are thought to have originated in the suisaka area in kaga, ishikawa prefecture, and were named “Suisaka” accordingly. However, this theory of its origin was proven incorrect when a ceramic fragment of iron glaze, supposedly from “Suisaka”, was found at the yamagoya kiln and the hyakken kiln etc. in the arita old kiln site. Although “Suisaka” featuring an iron glaze is now known to have its origins in arita, the name suisaka remains.
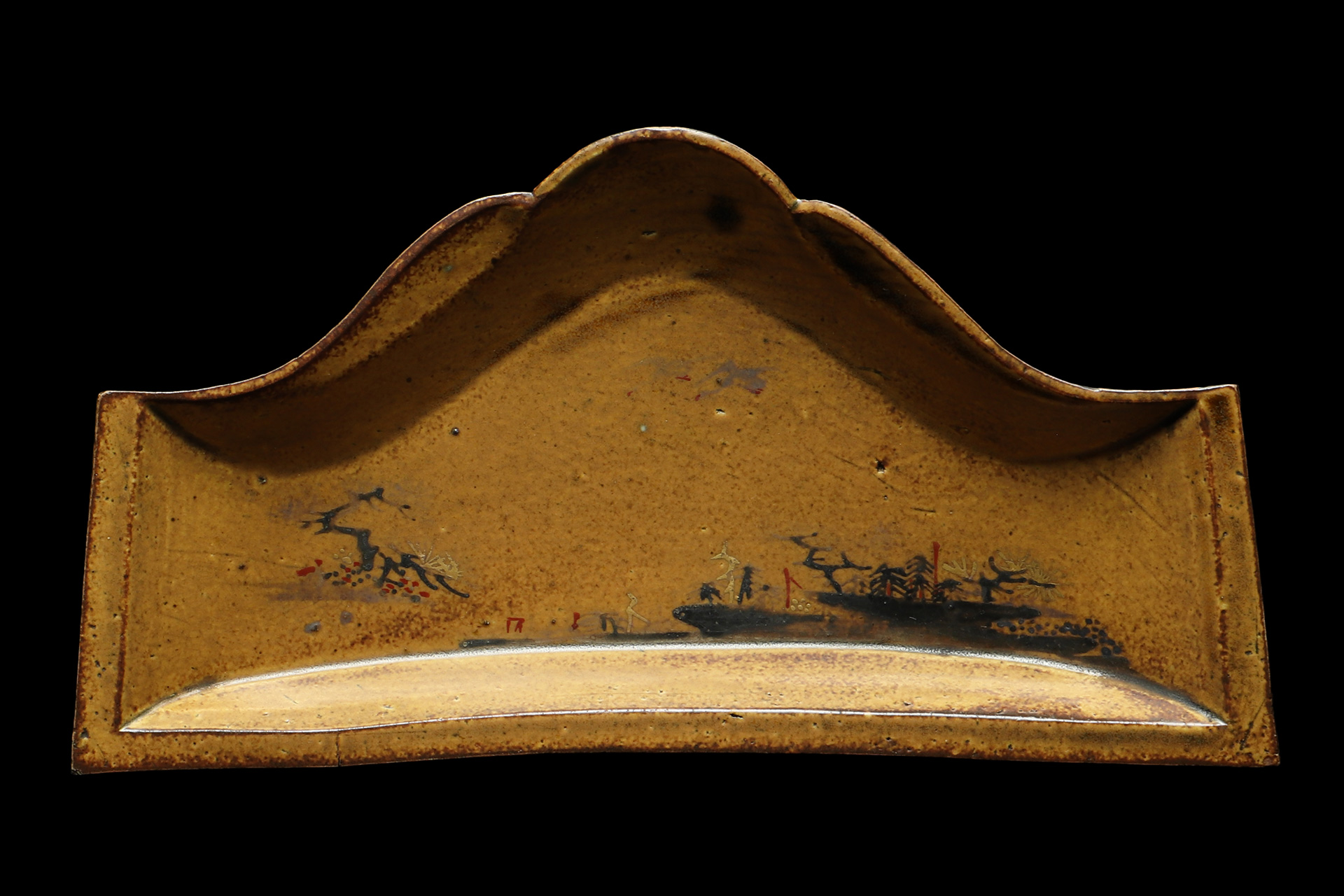
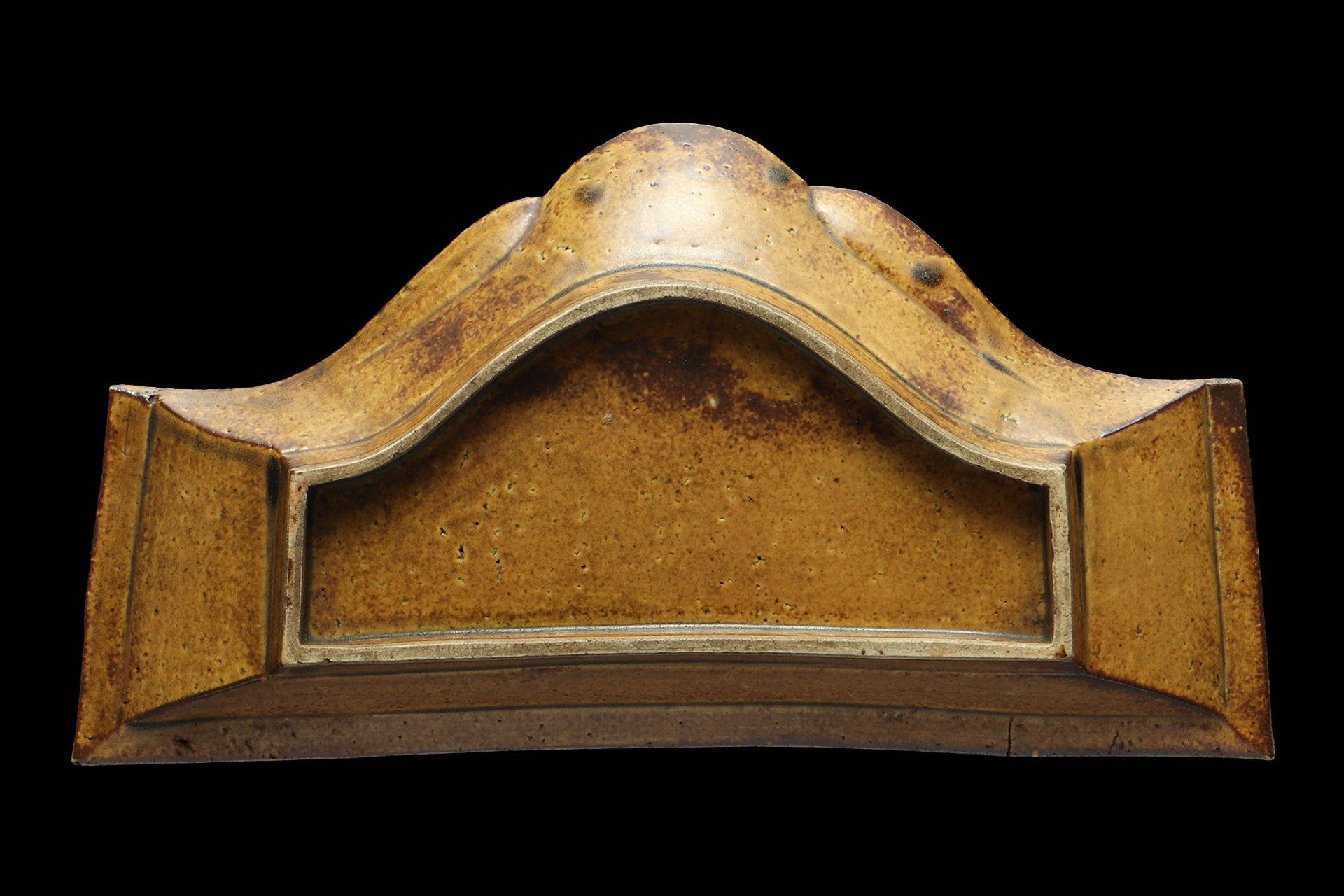
Kinginsai of Old-Kutani
Pottery fired using kinginsai, a technique of coloring with gold and silver, probably began in the Meireki era(1655-58)and made its way as far as europe, based on export records from the dutch east india company(VOC)and handed down pieces. The use of silver coloring declined in the 1670s. One reason may be that when coloring with silver, the silver oxidizes over time, eventually turning into a darker color. On the other hand, gold coloring became widespread from the Genroku era(1688-1704), the peak of old-imari exports, and flourished as the luxurious overglaze enamels and gold, which became the mainstream.
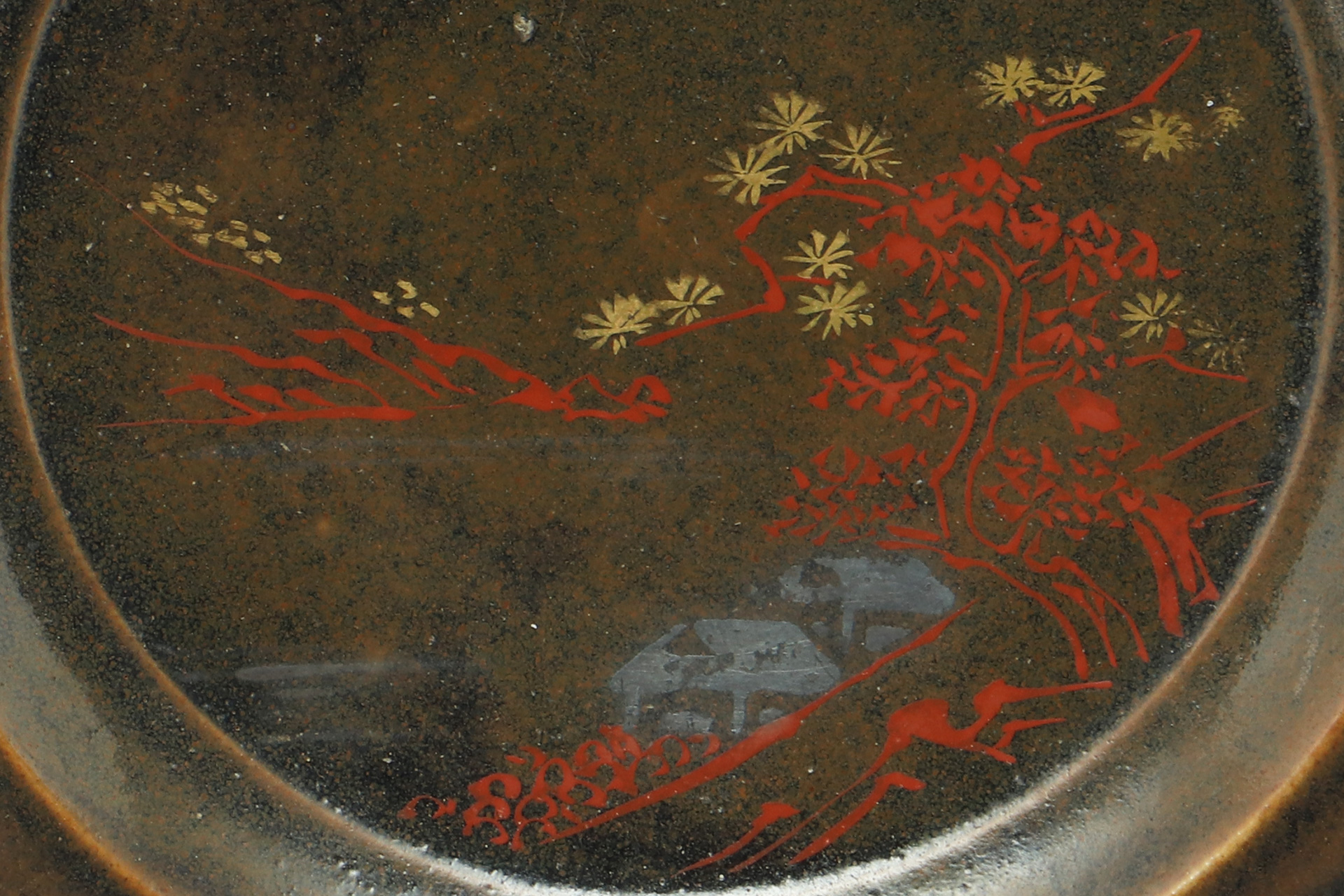
We sell and purchase Old-Kutani
We have a physical shop in Hakata-ku, Fukuoka City, where we sell and purchase "Old-Kutani" works. Drawing on a long career and rich experience in dealing, we promise to provide the finest service in the best interests of our customers. With the main goal of pleasing our customers, we will serve you with the utmost sincerity and responsibility until we close the deal.